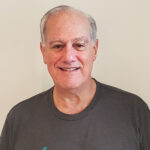
How You Can Improve the Performance of Your Vibratory Screener?
By Jack Steinbuch
We can all agree that the improvement of the performance of any production equipment is a good idea. That being said, we first need to establish the definition of the performance of a screener. I will go with any means to improve the screening efficiency to gain as much of the desired product with the least amount of contamination. We will make the assumption that the correct screener has been selected for the application, so now we will look for ways to improve its performance.
Read More…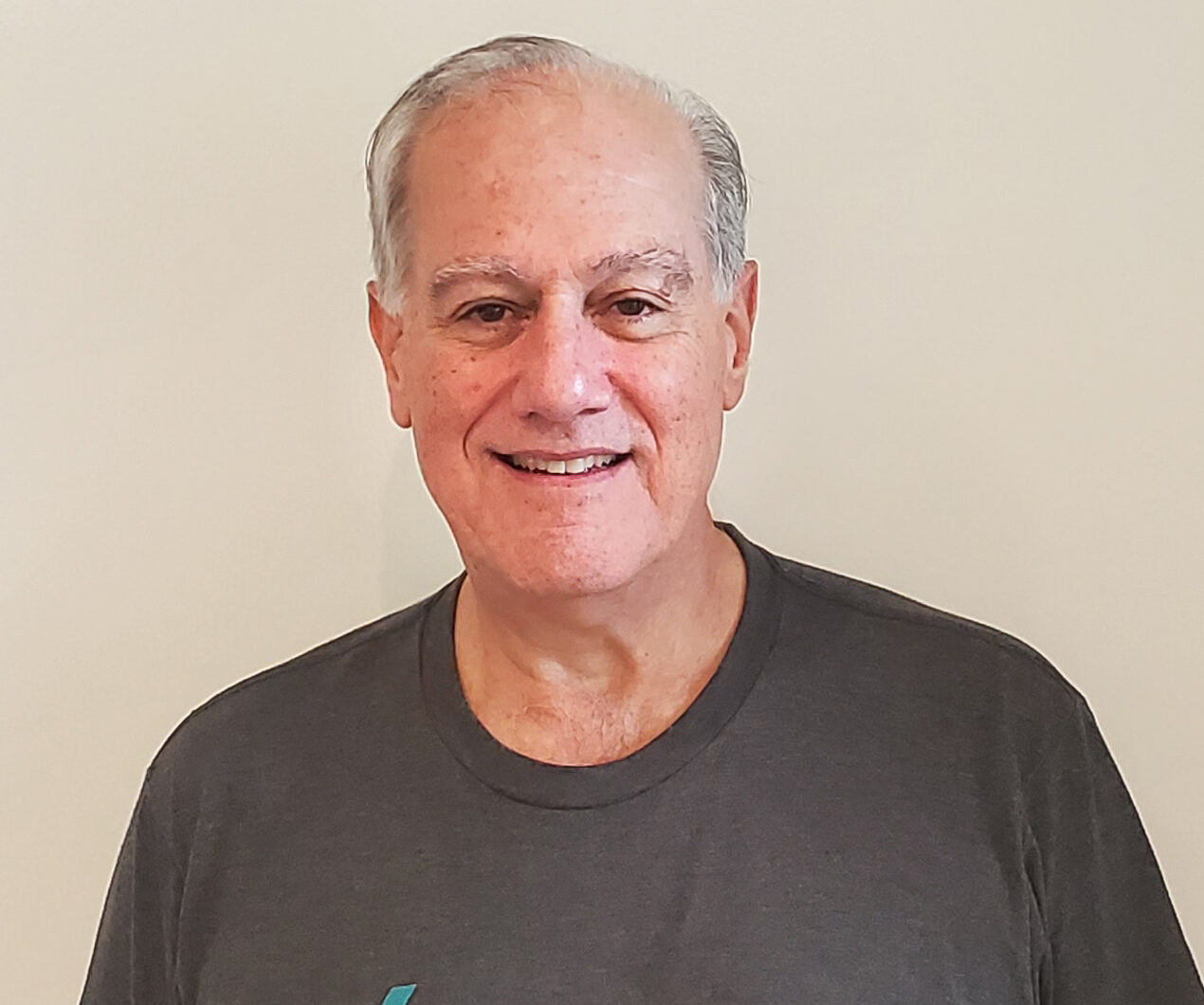
Jack Steinbuch has been with The Cleveland Vibrator Company for over 36 years accumulatively. He has previous experience in the manufacturing industry as a Senior Application Engineer and has worn many hats on our team in sales and managerial capacities. Now, he’s in the position of General Sales Manager. With a BSCE from The University of Toledo, he is an expert in the realm of sizing vibratory screeners and feeders, and sizing vibratory drives for tables and other vibratory equipment. Understanding that customer service is crucial, Jack believes it is important to provide the proper product for every application, even if it happens to not be supplied by The Cleveland Vibrator Company.
In his off-hours, you can find Jack spending time with his family and playing with his grandchildren. He loves sports; both watching and playing, and is an avid golfer and a league bowler during the winter. He will be retiring at the end of September 2021 and hopes to spend his winters vacationing in Florida.
Share this blog post: