Advanced powder screening technology needs are increasing for high-energy sieving screeners, calling for smaller particle sizes with stricter specification requirements. Industries that work with dense materials, such as 3D printing or additive manufacturing, need precise control over particle size for production. This contributes to maintaining the desired quality and consistency of the powder material.
The problem with high-density materials is their tendency to blind the screen deck when using traditional ultrasonic sieving solutions. Other screens deblinding solutions like sliders or ball tray decks don’t provide the efficiency to keep operations running smoothly.
The VertaBrute Series by HK Technologies is a cutting-edge powder sieving solution that provides numerous advantages to tackle these screen blinding challenges in your powder processing.
Boost productivity and cut costs and downtime in operations.
Simple design elements, such as quick screen changeover, keep powder processing operations moving. A screen frame securely holds a loose wire mesh cloth above a fixed wire mesh, eliminating the use of any adhesives on the screen deck. Operators can store a variety of screen mesh sizes in-house and can switch out the loose mesh screen at any time, providing the ultimate flexibility in powder processing.
With the quick screen changeover design element, minimal downtime is required between runs. Typically, users can easily switch out mesh screens in 20 minutes or less.
Compared to other screen deblinding solutions, like ultrasonics, wear and tear of the screens don’t shut down operations when they need repairing. Not only does this eliminate costly production downtime, but it saves on freight and rescreen charges when outsourced.
Get enhanced powder flowability.
Conventional ultrasonic methods involve directly vibrating the wire in the mesh separately from the machine, but this is generally ineffective for coarse or extremely fine mesh sizes and high-density materials.
High-energy screeners use strong vertical vibration to create deblinding action, making them more effective than traditional sieving technologies. As described before, the screen frame has a loosely fit wire mesh on top of a fixed metal mesh.
The high-energy vibration generated by the oversized rotary electric drives plays a crucial role in the functioning of the loose screen. When the material is loaded onto the screen, it is subjected to this intense vibration, which causes the particles to move vigorously. This movement prevents the material from settling down and instead keeps it elevated on top of the mesh
Furthermore, the high-energy vibration also helps prevent blockages or mesh clogging. As the material is constantly in motion, it is less likely to accumulate or get stuck in the openings of the mesh. This ensures a continuous and uninterrupted flow of material through the screen, enhancing productivity and reducing downtime for maintenance and cleaning.
This vibration also breaks up agglomerates or clumps that may have formed in storage or during handling. The action improves overall throughput, allowing for hard-to-screen materials like metal alloys, for example, to flow consistently through, boosting the reliability of the process.
Ensure efficient particle separation and increase throughput in high-volume processing applications
High-energy sieving machines, like the VertaBrute, are built robust enough to withstand the continuous flow of powder and the stresses associated with high-volume screening.
High-capacity sifting capabilities aim to maintain efficient and accurate particle separation and classification based on size, or removing over- and undersized particles, agglomerates, or foreign matter.
The oversized rotary electric drives are designed to produce a robust and consistent vibration that effectively agitates the material. This vibration is carefully calibrated to ensure that it is strong enough to keep the material in motion but not so intense that it causes damage or excessive wear to the screen or the equipment.
As the material experiences this high-energy vibration, it undergoes a series of complex movements. The particles are lifted and thrown upwards, creating a cascading effect. This constant motion prevents the material from becoming compacted or forming clumps, ensuring that it remains loose and free-flowing.
The elevated position of the material on top of the mesh is crucial for the efficient operation of the loose screen. By keeping the material elevated, the screen effectively separates it into different sizes or grades. The vibration causes the smaller particles to pass through the mesh, while the larger particles remain on top. This separation process allows for the efficient sorting and classification of the material based on size or other desired criteria.
This high-energy vibration not only prevents settling and compaction but also facilitates the separation and classification of the material. It ensures a smooth and efficient screen operation, contributing to improved productivity, higher production yields, and faster throughputs.
Design elements are the key to success and protect your bottom line.
The VertaBrute is affordable to own and maintain, making it a great investment option. The VertaBrute has a low cost of ownership and requires less maintenance than traditional ultrasonics because it has fewer wear parts. In-house rescreening capabilities eliminate costly and timely screen repairs and production downtime.
Design flexibility allows for various deck configurations including single, double, and triple decks, cutting and separating your materials to the size you need. Straight-through or vertical discharge of fines provides easy and in-line production flow.
All contact areas are constructed of 14-gauge 316 stainless steel, allowing zero contamination with a fully custom-sized base. Screen diameters include 30″, 36″, and 48″ that can screen down to 20 microns or 325 mesh on a 48″ screen.
The VertaBrute matches the capabilities of other high-energy screeners in the market, like the Elcan Hi-Sifter. However, HK Technologies designs and manufactures the VertaBrute in the United States with maintenance and customer service help located in Salem, Ohio. After buying our product, we aim to offer exceptional customer support, ensuring you feel confident that this equipment will work well in your facility.
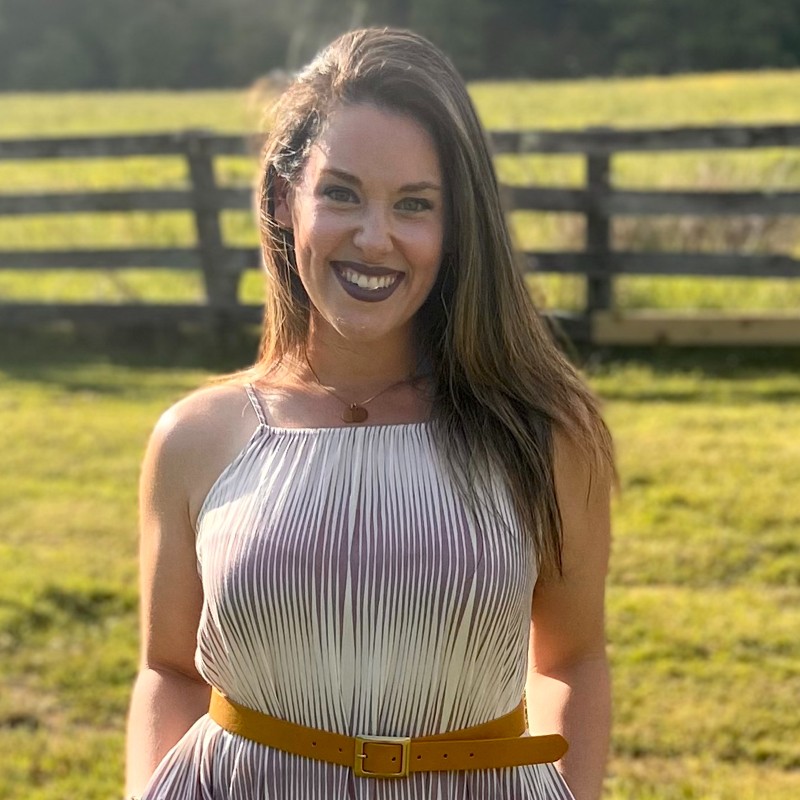
Katy Sabo has been the Industrial Vibrator Duchess of The Cleveland Vibrator Company since 2014. The originator of #VibrationEducation, Katy has helped create CVC brand awareness across the globe and has made it her personal priority to share the importance of Industrial Vibration with anyone willing to listen! When she isn’t shaking things up in the Marketing Department, you can usually find her shopping with her favorite sidekicks (she’s the proud mom of two little ladies), going on long walks/runs with her favorite furry family members, or rooting on any Cleveland team with her diehard fan of a husband.
Share this blog post:
Follow us: