“Bend, but don’t break” is an old football saying that refers to a defense that “allows” the opposing team to move the ball down the field on offense, but ultimately prevents them from scoring touchdowns. While it’s not a perfect analogy, you could apply this statement to recommending externally mounted vibrators to aid in the flow of material down hoppers, bins, and chutes without damaging the mounting surface.
Our challenge is to recommend a vibrator that will flex (bend) the wall or surface where it’s mounted to aid in the flow of material but not break it. Some people do not use certain external vibrators as they’ve had the bad experience of cracking the mounting surface. It’s easy to blame that style of vibrator, or vibrators in general, and look for some other method to get their material to flow. Here, I will explain how vibrators should be utilized without damaging the mounting surface.
The first step is providing enough vibrational force to flex the wall to get the material to flow. There are many factors to consider including the configuration of the hopper, bin, or chute as well as the bulk density and flowability of the material. Once a vibrator with the proper force is selected, you need to find out the recommended wall thickness for that vibrator which accounts for enough flexing to aid in the flow of material.
It’s quite possible that the force required is better suited for a wall thickness that is greater than the intended wall or surface where it will be mounted. We would then recommend reinforcing the wall with a plate that is heavy enough to withstand the force output of the vibrator, yet still, allow flexing. This reinforcing plate should be stitch welded to the surface with the corners left un-welded. A mounting channel is then stitch welded in the center of that plate with the end of the legs left un-welded. Where a plate is not feasible, angle runners can be stitch welded on both sides of the mounting channel legs (with the ends left un-welded) to distribute the vibrational force over a larger area to prevent cracking. Please note that we recommend stitch welding because continuous welds can cause the wall to break, especially at the corners where cracks will propagate at about 45 degrees. For those applications where the wall thickness is heavier than the force required, we recommend selecting a vibrator with enough force to flex the heavier wall.
Again, our recommendation is to flex the wall to promote material flow and follow good welding practices combined with wall thickness recommendations to prevent cracking. Additionally, most vibrators offer adjustable force capabilities, so it’s a good idea to begin at a lower force output and then increase it as necessary to promote proper material flow. This will minimize stress on the mounting surface and undoubtedly increase the “life” of the vibrator.
Want more information? Speak with one of our helpful Sales & Services Team Members today!
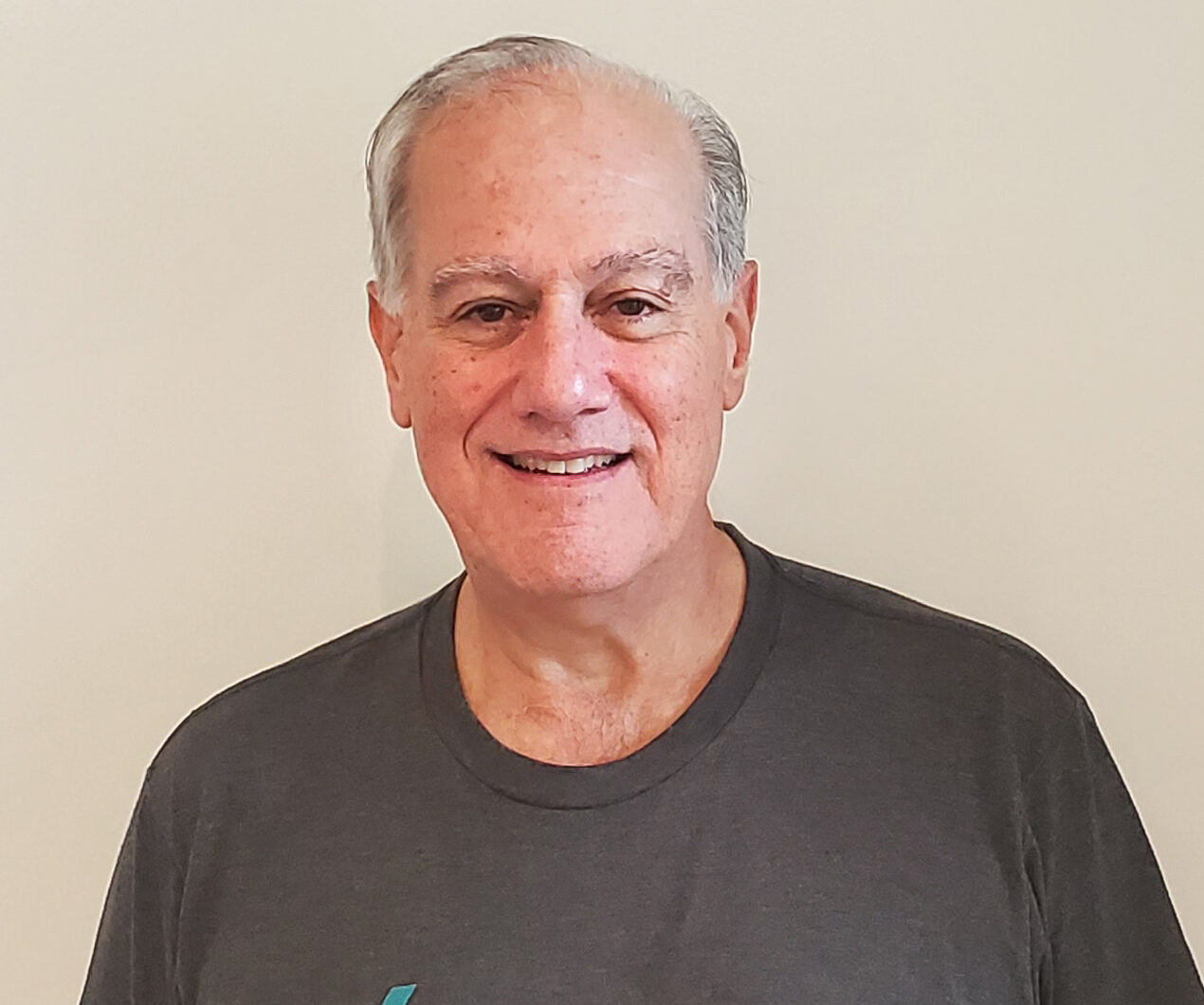
Jack Steinbuch has been with The Cleveland Vibrator Company for over 36 years accumulatively. He has previous experience in the manufacturing industry as a Senior Application Engineer and has worn many hats on our team in sales and managerial capacities. Now, he’s in the position of General Sales Manager. With a BSCE from The University of Toledo, he is an expert in the realm of sizing vibratory screeners and feeders, and sizing vibratory drives for tables and other vibratory equipment. Understanding that customer service is crucial, Jack believes it is important to provide the proper product for every application, even if it happens to not be supplied by The Cleveland Vibrator Company.
In his off-hours, you can find Jack spending time with his family and playing with his grandchildren. He loves sports; both watching and playing, and is an avid golfer and a league bowler during the winter. He will be retiring at the end of September 2021 and hopes to spend his winters vacationing in Florida.
Follow us:
Share this blog post:
2 Responses to Hopper Vibration – Bend, But Don’t Break!