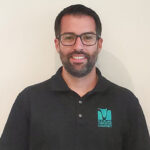
Air Powered Vibratory Feeders: 3 Things To Know Before Making a Buying Decision
By Mike Stratis
When it comes to handling dry or semi-dry bulk material, there are few means to transport the material from point A to point B. The common options are pneumatic conveying equipment, frequently dense or dilute phase, belt conveyors, screw augers or vibratory feeders, flat pan style, or enclosed tube style. There certainly is a time and place for each of these options but we will focus on the vibratory feeder design.
Companies looking to make a buying decision on which type of equipment to install that will handle the material typically turn to the vibratory feeders that are powered by a pneumatic or air piston vibrator for one of, or a combination of, these reasons:
Air Powered Feeders Work Well Within a Budget – First, and maybe most importantly, the purchase price. The air-powered vibratory feeders can be the low-cost alternative to the electromechanical or electromagnetic powered vibratory feeders. The biggest cost savings can come directly from the vibratory drive or mechanism and the vibratory controls. Electromechanical feeders typically have two vibratory motors while the electromagnetic feeders typically have one large vibratory drive attached. Each of these electric-powered options requires an electrical control box, with dual thermal overload protection for the electromechanical vibratory motors for on/off operation, speed control, or intensity of the vibration control. In contrast, the air-powered feeders are driven by a single non-impacting piston. For example, the Cleveland Vibrator VMSAC units are either controlled by a manual ball valve or 2-way, normally closed, solenoid valve.
Read More…
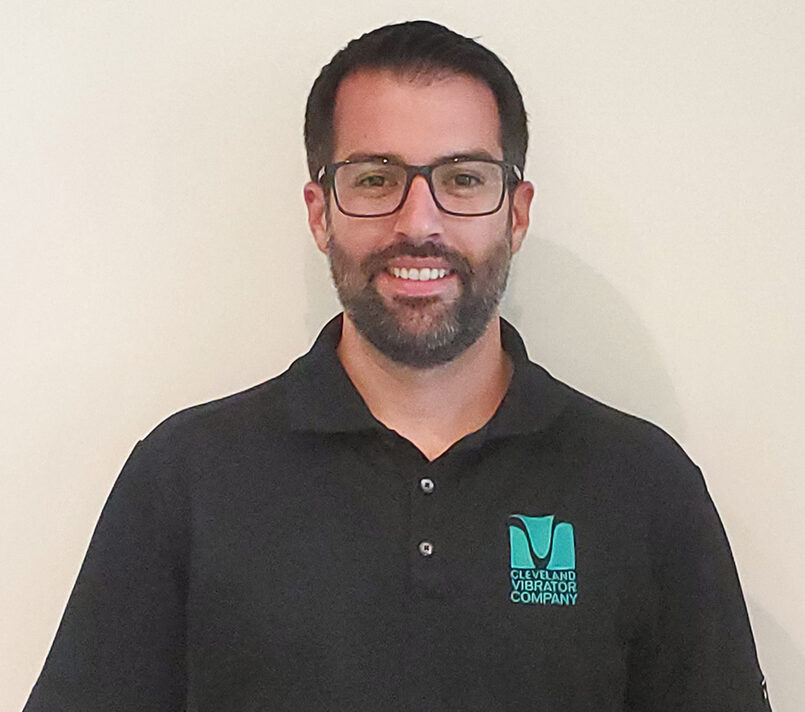
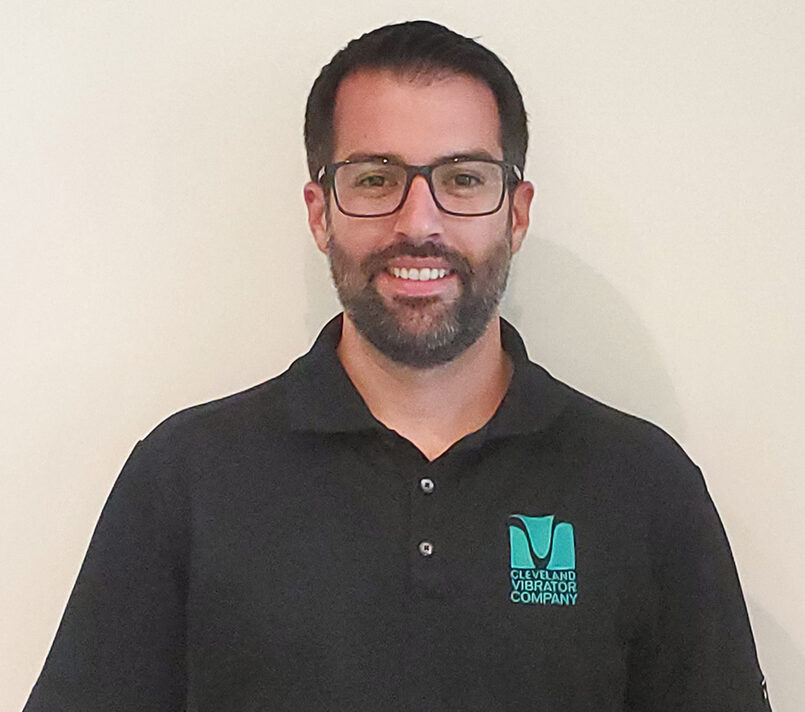
Mike joined The Cleveland Vibrator Company team in 2013 with prior experience in manufacturing sales with a Cleveland company in the tool and die industry. Now, he’s the Director of Sales and specializes in “making stuff that shakes stuff”.
When he’s not immersed in the world of industrial vibration, as rare as that might be, Mike keeps busy *not finishing in last place* in Fantasy Football and enjoys spending time with his wife and three kids. It’s always golf season for Mike, and he’s been known to 3 putt his way around any course and can roll tee balls in rain or shine. You can find him tailgating in the Muni Lot before Browns games or supporting local breweries.
As an avid provider of #VibrationEducation, he offers this free bit of advice, “Not all vibration is the same. Force and frequency do matter!” However, there is a 2% upcharge for all Michigan and Steeler’s fans.
Share this blog post: