Over the years I have handled hundreds of sales calls. Some are looking for new equipment while others are looking to improve upon an existing application. The majority of the customers who are not looking for new equipment want to increase their “yield” or “productivity” of the final product they are trying to produce. My first question when addressing their issue is what is the percentage of “good” product are they losing in the oversize material in their screener? While some have a good idea of this amount others have no idea what the correlation between yield and oversize has to do with each other.
Recently a customer came to me requesting a quote for a 48” diameter vibratory screener. He said he was losing too much “good product” in his oversize which caused him to rescreen his oversize once and sometimes twice. While I would gladly sell him a larger screener, I first asked him to describe his screening process – not to go into too much detail – his final product was a -80 mesh +120 mesh alumina oxide powder and he was losing 30% of -80+120 product in his 80 mesh oversize. I asked him why he thought he needed a larger screener? His response was this was what his current screener manufacturer recommended. They stated he simply needed more surface area to increase his product yield. While that statement is generally true and is a great way to sell new equipment, there ARE other alternatives.
After receiving a sample of the customer raw product (prior to being screened) I found there is a very high percentage of +80 mesh material – over 50%. Actually, the majority of the 50% material would not pass a 60 mesh. After an initial sieve analysis, I mixed the material back to its original state then I screened the material over an 80 mesh then 120 mesh and checked my yield. The customer was pretty close – he was losing 25-30% of good material in his process. My second test removed the +60 mesh material out of the raw product then I repeated the -80 +120 trial. Shazaam! We were able to increase his yield substantially – reducing the amount of “good product” in his oversize to less than 5%. Another positive result came out of this process change – the customer’s overall throughput rate went up approx 15%. Basically, he was able to run the -80+120 screener at a faster rate since removing the =60 mesh material.
Well, you’re probably thinking – “the customer still needs to buy another screener to screen out the +60 mesh material……..”. Yes, that would be an option but a less costly option than a new 48” diameter screener would be to utilize a smaller diameter screener for this cut. In this case, the customer had another screener where he was able to pre-screen on the 60 mesh and then cascade his product to the double-deck 36” screener he was currently using. Another solution would add a 3rd deck to his existing 36” diameter screener. Although I am not a fan of 3 or for that matter 4 deck screeners – they require too much time assembling, cleaning, and re-assembling – just ask your maintenance guys! Another option to consider is using any vibratory feeding system currently in use. Turn the feeder into a feeder/screener and kill two birds with one stone. I will discuss that process in another blog so stay tuned!
Want to see these fine mesh screeners in action? Check out our YouTube Channel!
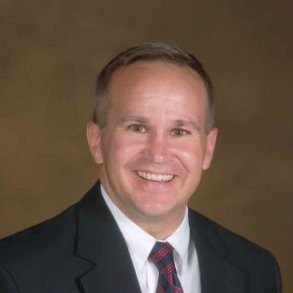
Jeff Hochadel has over 25 years of experience building and selling vibratory screening equipment. Jeff is responsible for handling fine mesh screening applications for The Cleveland Vibrator Company. His expertise is utilizing our Ultrasonic Deblinding System to solve difficult screening problems. When Jeff is not visiting customers promoting our products you can most likely find him fly fishing.
Follow us:
Share this blog post: