Several weeks ago, I was reading an article in one of the technical journals discussing the variety of ways to eliminate screen blinding on vibratory equipment. The article discussed a number of “old school” solutions such as rubber balls, clean rings, spray nozzles and brushes. These methods have been around for decades and produce a low to moderate level of success in keeping the screen surface from blinding or clogging. The article also discussed the most effective solution for screen deblinding – Ultrasonics. While it is the most effective, ultrasonic deblinding systems are also the most expensive. If you are not familiar with ultrasonics the process involves sending out high-frequency vibration to the screen surface which basically agitates the mesh wire while reducing surface tension allowing fine particles to fall through mesh openings (or holes) while not blocking or clogging the openings. My last post provides some further description.
While trying to come up with a solution to a fine mesh screening application that would not allow for the use of stainless steel wire mesh (the product could not come in contact with any metallic surfaces) we tried rubber balls mounted under the screen frame but this was only successful for maybe an hour before the screen blinded over. We experimented with brushes – no luck. Ultrasonics was not an option since sonics cannot work with non-metallic mesh (such as polyester or nylon). My plant manager/mad scientist (who happens to be my brother) called me back to the lab to show me something interesting. He had taken one of Cleveland Vibrator Company’s mini turbine (Turbomite) vibrators which he had mounted to a pad and sandwiched this to our nylon screen surface. When he turned on the air to the vibrator the 20,000 vpms generated a tremendous high-frequency vibration sent out across the screen surface. The powder he had placed on the surface passed right through the mesh with no clogging or blinding. We then installed the screen frame in our vibratory screener (a 36” dual drive vibratory screener) and ran the set up for several hours with no screen blinding. My plant manager looked at me and said “I think you can sell this!” Since that time we have sold a number of these “anti blinding” devices solving some challenging applications that involved the application described above, wet ceramic slurry applications, and screening applications in hazardous “explosive environments”. We have also sold the Turbomite Deblinding System (TDS) attached to a screen deck only and placed over a drum or container for simple check screening applications. I have included a couple of pictures showing the TDS. To see if the Turbomite Deblinding System can work for your application, please contact us.
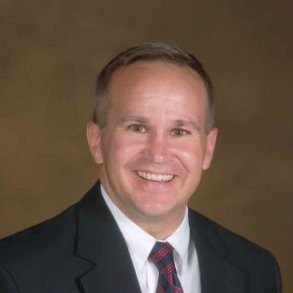
Jeff Hochadel has over 25 years of experience building and selling vibratory screening equipment. Jeff is responsible for handling fine mesh screening applications for The Cleveland Vibrator Company. His expertise is utilizing our Ultrasonic Deblinding System to solve difficult screening problems. When Jeff is not visiting customers promoting our products you can most likely find him fly fishing.
Follow us:
Share this blog post: