Stroke, Frequency and Force: The Keys to Vibratory Compaction
By CVC Team
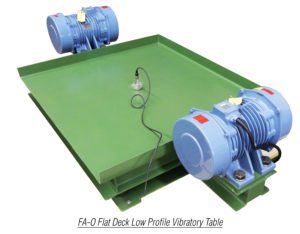
One of the more common applications for industrial vibration is settling or compacting a wide variety of products with a vibratory table. Compaction applications range from foundry sand around a core to powdered metal, beer bottle caps, individual sugar packets, ceramic mixes, to concrete blends used in ATM wall enclosures.
There are many vibratory equipment options available that will effectively settle and compact your material, including:
- Vibratory Joggers (VJ)
- Pneumatic or Electric Powered Vibratory Packers (VP)
- Flat Deck Tables (FA)
- Grid Top Tables (GT)
- Vibratory Belt Tables (BT)
Regardless of the equipment, we start by understanding the material and working with a few basic parameters
The most critical parameters in any compaction project are vibration frequency, and the amount of force applied. These two parameters drive the third parameter, stroke or displacement. Heavier materials respond best to high-frequency vibration and the resulting smaller stroke that high-frequency vibrators produce. Lighter material or discrete parts often compact best with a lower frequency vibration and a larger stroke. Typically, we start testing a product at a given frequency based on bulk density and adjust the force to load (g’s) ratio to get the best compaction results. With the wide range of vibrators at our disposal, we can choose from air-cushioned pneumatic vibrators (VMSAC), rotary electric (RE) vibrators, or electromagnetic (CM) vibrators that best suit the frequency and force requirements.
Read More…Share this blog post: