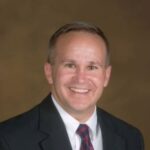
The Importance of Product Testing for Fine Mesh Screening
By Jeff Hochadel
Many times a potential customer will call our office or email asking for a quote and delivery on a specific type of equipment. Our standard response involves asking the customer a series of questions ranging from what the product is, estimated throughput rates, percentage of plus and minus screen size, and others. We typically also ask for an application data sheet to be filled out. All this helps remove the guesswork out of equipment sizing. Sometimes the customer thinks he knows what is required based on past experience or what someone else has told him he needs. While many times these assumptions may be correct, we want to make sure what we sell the customer will ultimately meet or exceed their expectations. While filling out forms and asking questions definitely assists in proper screener selection, I have found asking for a sample of the product for in house testing eliminates all the guesswork out of the equipment selection process. If time permits and the customer requires we can also send out a demonstration model for a short in-house testing period.
Running tests on a sample or sending out a demonstration model will ultimately remove all the guesswork out of equipment selection. Read More…
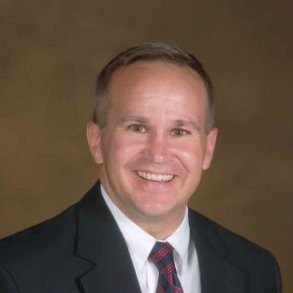
Jeff Hochadel has over 25 years of experience building and selling vibratory screening equipment. Jeff is responsible for handling fine mesh screening applications for The Cleveland Vibrator Company. His expertise is utilizing our Ultrasonic Deblinding System to solve difficult screening problems. When Jeff is not visiting customers promoting our products you can most likely find him fly fishing.
Share this blog post: