When I joined the Cleveland Vibrator family, I had just graduated with a Bachelor’s degree in Mechanical Engineering and had no prior experience in the field of industrial vibration or vibrators. During the course of my formal education, I had one class that dealt with vibration, the focus of the class as I recall was how to eliminate it, certainly not how to use it to perform meaningful work. When I was hired on, my informal education into the world of industrial vibrators and vibration began. Just like coming into any family, you learn the way the family works, the teams they root for, the legends they admire and the folks to be avoided. I feel fortunate that I had some excellent family members to bring me up in the world of vibration.
When it comes to vibratory equipment there are many ways to introduce vibration into a structure and produce the desired results. You may be looking to use vibration to move bulk material from point A to point B, screen large particles from small or compact more material into a box. These sources of vibration might include electromagnetic vibrators, belt-driven shakers, rotary electric vibrators, crank arm mechanisms, pneumatic piston vibrators, two bearing unbalanced belt-driven shafts or natural frequency two-mass systems.
Since I’ve been a part of the Cleveland Vibrator family there have been two primary sources of vibration for our equipment:
- Rotary electric vibrators
- Pneumatic piston vibrators
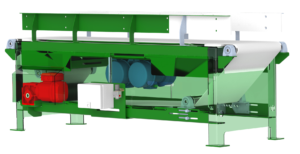
Transparent rendering of a Cleveland Vibrator Model BT Vibratory Belt Table powered by (2) Uras Techno Rotary Electric Vibrators
The Family has schooled me in the benefits of rotary electric vibrators for equipment over a belt-driven shaker or electromagnetic vibrators. I’ve learned to design compact and effective equipment powered by quiet air-cushioned piston vibrators with their linear motion. Jack Steinbuch has been instrumental in my family education. Interestingly, Jack came to the Cleveland Vibrator family after being indoctrinated in the business of industrial vibrations by another ‘family’ that preferred to use unbalanced pulley systems and ‘two bearing’ circle throw machines. I’ve heard it said that when an individual converts from one line of thinking or philosophy to another, they’re often a staunch believer in that new way of thinking, more than a person that was raised in that school of thought. I think that’s the case with Jack and the uses of rotary electric vibrators on vibratory equipment, he’s a True Believer.
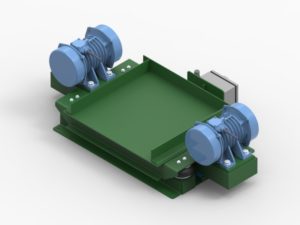
Cleveland Vibrator Model FA-O Low Profile Vibratory Compaction Table powered by (2) Uras Techno Rotary Electric Vibrators
As we’ve talked about before various materials respond differently to different combinations of force and frequency, one size does not fit all. Using rotary electric vibrators, it’s pretty easy to get any combination of force output and frequency that might be required for optimum results. Let’s say that you want to construct a vibratory table such as a flat deck (FA) model where the goal is to vibrate the structure and the product at 3 g’s of acceleration. In theory, we could select an appropriate pair of rotary electric vibrators with an operating frequency from 3600 rpm (2 pole) to 900 rpm (8 pole). Any choice impacts the performance of the unit and in the end, the results produced by the vibratory table. For example, let’s look at using a pair of RE 6-2 vibrators to drive the table. Assuming all things are equal and we produce 3 g’s with this vibrator, structure, and product combination, what happens to the amplitude of vibration?
For the 2 pole vibrators, we’d expect to see an amplitude of vibration of 0.016”. This would be a straight line peak to peak movement of the table. How would that compare with a pair of 6 pole vibrators running at 1200 rpm? Again, assuming the same 3 g’s of acceleration but at the slower rpm, the resulting stroke we would expect to see is 0.147”.
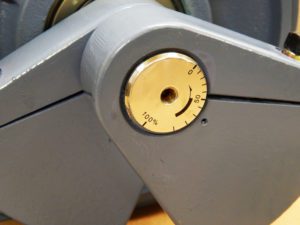
An Inside Look: The eccentric weight on a Rotary Electric Vibrator
There’s a significant difference in the resulting stroke or movement of the vibratory table, typically this difference in stroke would generate totally different results when trying to compact a given product. It’s pretty easy to see the flexibility afforded to the equipment designer when working with rotary electric vibrators. In addition to the range of vibrator speeds, the rotary electric vibrator offers flexibility in force output. The adjustable weights can provide the designer with 0 to 100% of the listed force output depending on the positioning of the eccentric weights, again something that is near impossible to accomplish with other sources of vibration.
I understand that this is ‘the family’ I’ve worked in for more than a while, but I have looked at and worked with other options to introduce vibration into a structure. As an equipment designer and problem solver, it’s pretty hard to beat the flexibility and options available when you use rotary electric vibrators. Recently, I had an opportunity to sit down and talk with another manufacturer of vibratory equipment. Their family tradition is to use a belt-driven off-balanced shaft to vibrate their screeners. Their goal is to produce smarter, simpler equipment yet they talked about the many challenges they were experiencing with their off-balanced shaft. These issues included bearing failures, additional costs to provide a constant stream of oil to the bearings, increases in maintenance costs, and increased costs of components such as pulleys, sheaves, and drive motors.
When you think smart and simple you’ve got to think rotary electric vibrators:
- You get many options in operating frequency and force output with easily adjustable weights to further tailor that force output to your requirement.
- Maintenance is very simple, a number of vibrators are permanently lubricated so there is no need to provide oil or even additional grease.
- On the larger units, there are grease fittings that require periodic attention, easy to get a standard grease gun and grease when required.
- Safety! There are no belts or exposed moving parts, eliminating the need to put guards on belts or pulleys.
If you’re involved with vibratory equipment or industrial vibrators, I’d encourage you to look at the options and flexibility available when you choose the path of Rotary Electric Vibrators. Who knows, maybe you’ll be a convert as well! The entire family here at Cleveland Vibrator, sales and engineering, is happy to assist with the selection of an appropriate rotary electric vibrator for your demanding application, please don’t hesitate to reach out; we’re always looking for new family members!
Share this blog post:
Follow us: