OSHA specifies that a hearing conservation program should be in place when “noise exposure is at or above 85 decibels averaged over 8 working hours, or an 8-hour time-weighted average (TWA)”. This can be an issue for some vibratory equipment. However, we have selections available that will reduce noise levels which can result in many positives for your facility (OSHA).
For example, did you know investing in noise-reducing vibration can lead to an increase in productivity and overall safety? High noise levels can lead to short- and long-term physical damage including ringing ears, temporary changes in hearing, and long-term hearing damage or loss. But, less commonly known, it can also put a strain on your pocket by reducing productivity, contributing to poor communication and concentration, and can even contribute to workplace accidents by limiting your employee’s ability to understand speech (OSHA).
Since there is a wide variety of vibratory equipment, for this blog, we will focus on “brute force” vibratory equipment. The vibrating body is directly installed on the equipment and is driven by a vibrator or dual motors, and the supporting structure is isolated from the vibrating body. Now let us look at potential ways to reduce their noise level:
The two drive power sources we will examine are electric and pneumatic. Electric is far more popular than pneumatic typically due to availability and/or conservation of compressed air and noise level.
Rotary Electric or Motor Vibrators
Brute force vibratory equipment commonly utilizes Rotary electric or motor vibrators. They have a shaft with eccentric weights typically on both ends that produce centrifugal force. These vibrators alone generally emit noise levels well below 85 dBA. Generally, mounting the vibrators on the equipment will increase the noise level, especially when it is running material.
Pneumatic Powered Vibrators
Pneumatic powered vibrators produce higher noise levels depending on the design. We typically offer piston vibrators for our vibratory equipment and use the air-cushioned design where the piston does not impact. This helps reduce noise levels as there are several sizes that are at or below 85 dBA. Additionally, you can install a muffler in the exhaust port to reduce noise levels. I learned from exhibiting at trade shows that for extra noise reduction, you can remove the muffler and run an airline from the exhaust port away from where workers are located and attach the muffler to the end. This combination will provide improved noise reduction for an air piston vibrator drive.
Noise Reduction Solutions for Vibratory Feeders & Screeners
With vibratory equipment like feeders and screeners, the material that is being fed will likely increase the noise level. Consider urethane, UHMW, or rubber fabricated liners for noise abatement on your vibratory feeder when handling nosier materials such as metal parts or billets. These types of liners have the added benefit of providing certain levels of abrasion resistance. The softer the liner material or lower durometer will improve noise reduction, but may have less abrasion resistance.
On screeners, you may want to consider alternative screening media to the more common woven wire cloth or perforated plate for noisier feed materials. For example, there are polyurethane, rubber, and rubber-clad perforated plate decking. These will reduce the noise level, but keep in mind that most have much less open area than wire cloth. There is also plastic mesh and coated wire cloth, although they may not be as suitable for installation in a vibrating screener.
Noise Reduction Solutions for Vibratory Tables & Packers
Other brute force vibrating equipment that handles loads includes a variety of vibrating tables and packers. This equipment is typically used to pack or settle dry material in containers or consolidate or de-aerate castable materials like concrete and refractories in molds. The tabletop does not have an attached container for most packing and settling applications. The container is essentially free to “bounce” on the vibrating deck, but it could be passively restrained. This would of course increase the noise level dependent on the type of container.
Air Mounts & Noise Reduction Solutions for Containers
Bulk bags and cardboard containers like Gaylords would have less influence on increasing noise levels than containers on a wooden pallet. Those palleted containers would have less effect than metal containers like steel drums. For metal containers, a liner made of urethane or UHWM on the vibrating deck would prevent metal on metal contact. This would reduce the noise level. You just need to avoid softer or low durometer material which might absorb too much of the vibrational force. Your goal is to prevent metal-on-metal contact without losing the necessary vibration energy to pack your material. The molds are fixed to the tabletop for many castable material applications. This provides the desired effects for de-aerating and additionally should prevent metal on metal contact.
Lastly, the type of isolators can also play a role in the noise level. You can reduce noise levels by using base mounted or cable suspended rubber isolators or inflatable air mounts instead of coil springs. Please note that even with coil springs, the noise can be reduced by using rubber or urethane inserts in the spring cups (holders) for base mounting or the top and bottom of the hanger box for cable suspension.

You are now fortified with some noise reduction ideas that you can try to implement with your vibratory equipment! These techniques can help keep your operation up to standards and your employees safe from physical injury. While making your purchasing decision, our application specialists are here to offer valuable assistance for your vibratory solution.
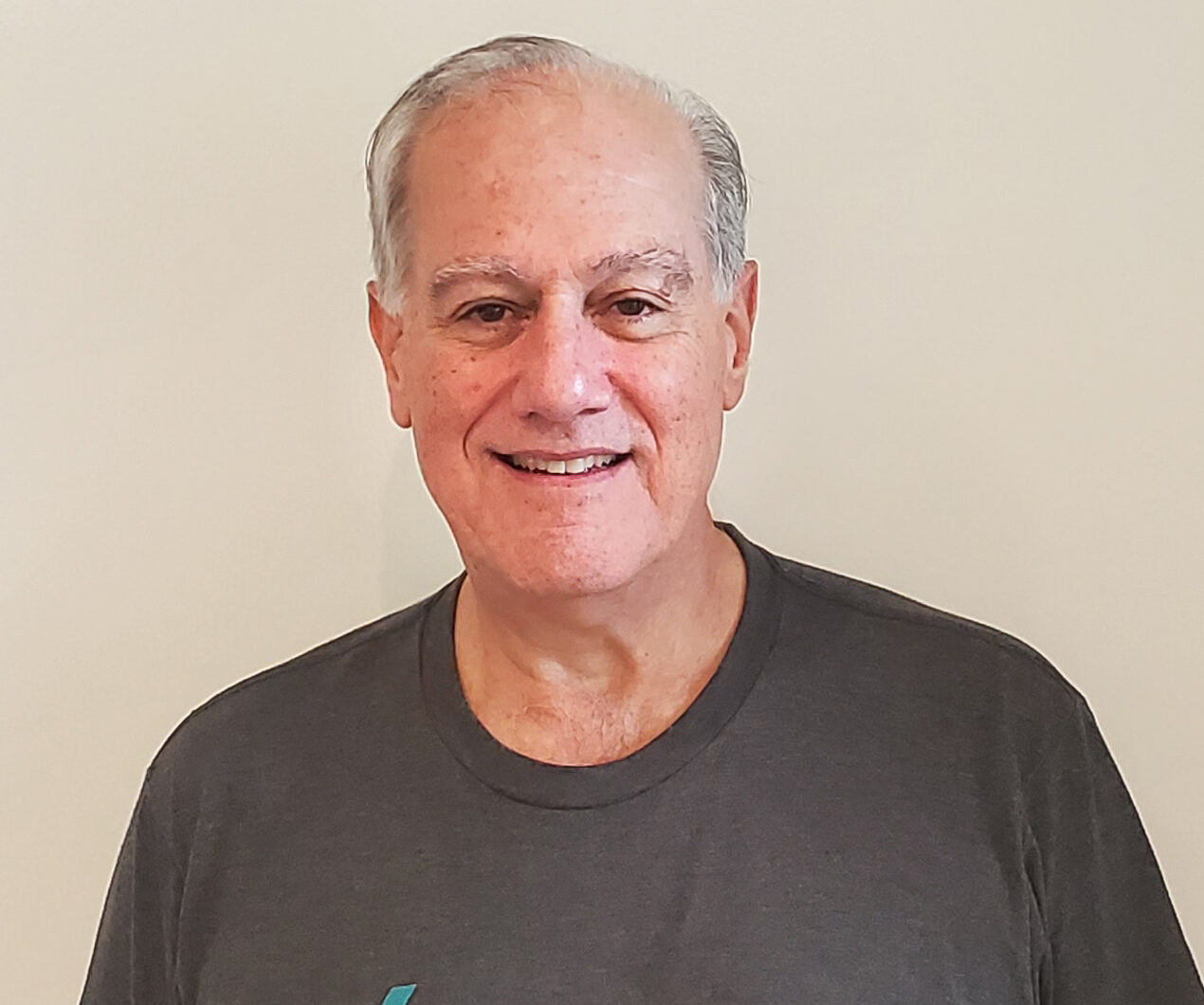
Jack Steinbuch has been with The Cleveland Vibrator Company for over 36 years accumulatively. He has previous experience in the manufacturing industry as a Senior Application Engineer and has worn many hats on our team in sales and managerial capacities. Now, he’s in the position of General Sales Manager. With a BSCE from The University of Toledo, he is an expert in the realm of sizing vibratory screeners and feeders, and sizing vibratory drives for tables and other vibratory equipment. Understanding that customer service is crucial, Jack believes it is important to provide the proper product for every application, even if it happens to not be supplied by The Cleveland Vibrator Company.
In his off-hours, you can find Jack spending time with his family and playing with his grandchildren. He loves sports; both watching and playing, and is an avid golfer and a league bowler during the winter. He will be retiring at the end of September 2021 and hopes to spend his winters vacationing in Florida.
Share this blog post:
Follow us: